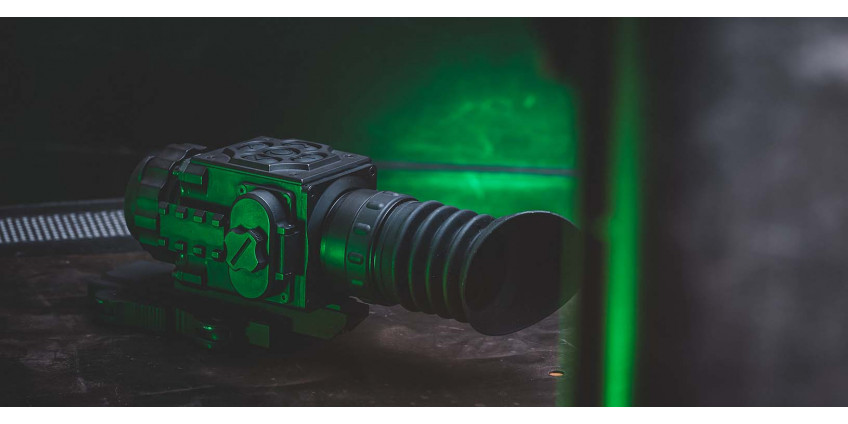
Night vision devices can be purchased at a store or online, in our century they became not just a military prerogative. Such devices are quite accessible to hunters, wildlife watchers, and those who need to see in the dark. Visually, they seem to be simple, many people think that NV accessories consist of lenses and an electronic part. But in fact, all night vision devices have a complex design, some elements of which are assembled by hand only. So, how night scope is made?
Raw Materials
The core part of the scope is the image intensifier tube (IIT). This element is located inside the device. Depending on the model of the scope, it can be of different diameter and size. The body of the IIT is made of different materials. To hold all elements together, indium, aluminum, or chrome is used. The assembled IIT is placed into a plastic boot. This method allows protecting it from shock, dust, and other undesirable factors.
Such isotope as tritium is also used in NV devices. This chemical element calls a lot of controversies and some people think it can cause cancer. So, are tritium night sights dangerous? Tritium does have radioactive radiation, but it’s very weak. Its beta-particles quickly decay and turn into helium-3. Helium-3 is not radioactive.
The penetrating ability of tritium beta-particles is very low, they cannot pass through a sheet of paper, clothe, and even the skin. That is, tritium has radioactive radiation, but it is very weak and is not able to accumulate in the air or anywhere else. Therefore, its use in night vision devices is permissible. Tritium is used in wristwatches and various signs in public places.
Design
You may have noticed that there are several pairs of lenses in night vision devices and any modern optics too. If in usual day-optics this is necessary to enhance clarity and increase the range, in NV devices lenses have a completely different task. Outer lenses, or objectives, collect all available light. In NV devices the lenses work as a focusing element, the light passes through them and is directed to the IIT.
The tube is responsible for that you could see a clear picture in almost complete darkness. Its construction is very complex, and it consists of:
· Photocathode. It accumulates the light, and its task is to turn cathodes into electrons.
· Energy source.
· Plate. It has a multichannel structure and is needed for increasing the number of passing-through electrons hundreds of times.
· Phosphor screen. Converts an electronic invisible image to an eye-visible picture.
Let's take a closer look at the plate. This invention became a real breakthrough in night vision device development. There are hundreds of microscopic holes on its surface, but they all should be of the same diameter and at the same distance from each other. The more the holes, the sharper and brighter the final image will be. So, electrons passing through the tube are hitting the plate. Due to this, their number increases hundreds of times in one second. In modern models of NV devices, there can be up to 10 million holes on the plate. Think about how many electrons they can create and how high-quality the image will be?
The stream of electrons is then passed to the phosphor screen. Thanks to a special coating, the screen catches the electrons and turns them into green light visible to the human eye. Due to this, we can see objects of different sizes and illumination, but all of them will be displayed in green color. Newer models of NV devices have high sensitivity to light, therefore, they can clearly show objects in almost complete darkness.
The Manufacturing Process
When manufacturing scopes the biggest part of the time takes IIT assembling. About 400 short processes are needed to make this core element. Of course, we will not talk about each of them separately, but divide the entire production process into several main stages:
· The base for the whole process is a round glass plate. Usually, the manufacturers buy it from a subcontractor. The glass blank is coated with gallium arsenide and heated.
· Then starts the process of “building” the microchannel plate. First, a glass ingot is placed in a special furnace. The furnace is heated up to 500 degrees. Due to the high temperature a glass drop forms at the bottom of the ingot. It falls down, stretching into a thin glass thread or a fiber. The machine then picks these fibers and twists them into hexagons. Therefore, the structure of the plate resembles the structure of a honeycomb.
· The gotten fibers are then heated and pressed to tightly bond them together. The obtained plate is then treated with a special acid, which removes the top layer of the glass. This allows opening all microscopic channels on the surface of the plate. The finishing touch – the plate is coated with aluminum oxide on both sides.
· Now it’s time for the screen to install. Usually, manufacturers buy a ready-made blank and do not make it themselves. The screen is treated with a solution of water and phosphor, and then the water evaporates, leaving the only phosphor.
· All finished elements are placed in the tube body by hand. There is a special room for this, clean and completely sterile. When assembling the tube, there should be no dust, drops of water, etc.
Then the air is removed from the tube, all elements are in a vacuum space. After quality checking, the tube is used in night vision devices – scopes, goggles, and others.
Quality Control
The IIT needs to be checked at every step of production. For this aim, manufacturers use special calibration equipment. It allows workers to check the diameter and thickness of the microchannel plate, as well as other parameters. If the part does not meet the requirements, they do not work with it further until it will be fixed. Calibration equipment is also checked regularly.
If the tube is made for standard night vision devices, it can be tested for shock or vibration resistance. Military accessories are often tested under high temperatures and humidity.
Remember that only quality accessories will ensure a pleasant use. Therefore, we recommend buying such devices from a trusted vendor. This will make your hunting or wildlife watching a success by any visibility.